News
Fact sheet about agric machines in Ghana
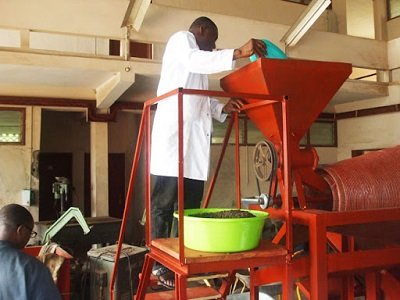
It is interesting to note that:
- Diesel/kerosene fired dryer was released in 2014. This is a dryer that employs indirect heating for drying grains and for processing food. It is applicable in all maize growing areas in Ghana.
The dryer is suitable for crop grain drying and for food processing; atomiser is locally manufactured; does not use exhaust fumes for drying. The technology reduces postharvest losses.
- Walk-in hot air cabinet dryer was released in 1993. The walk-in hot air cabinet dryer is available in four sizes 56 trays, 84 trays, 100 trays and 140 trays.
The dryer uses electrical energy as its source of fuel and has automatic temperature control system and a 24-hour timer to predetermine period of operation.
It is applicable in all cereals, root and tubers, and fruits growing areas in Ghana. It is used for drying of food commodities such as roots and tubers, vegetables, fruits, cereals, etc.
- Micro-nutrients fortification mixer for dietary supplementation for malnourished community was released in 2007.
The technology is for fortification of food with vitamin premix for malnourished children and women in Northern Ghana.
It is applicable in Northern Ghana. It is used for improvement of nutritional status of rural communities of northern Ghana.
- Snail meat preservation was released in 1995. The technology describes a more hygienic, appropriate and low-cost method for the preparation, spicing and solar dehydration of snail meat.
A second technology developed involved spice extraction and snail meat preparation for the corning of snail meat in brine. It is applicable in snail rearing communities.
It is used for snail meat preservation (solar dehydrated and canned) to offset scarcity of the product during the dry season when snails are scarce.
- Palm kernel shell separator was released in 2012. The technology reduces time for kernel shell separation from 24 hours per 60 kilogramme material to seven minutes per 60 kilogramme material.
It eliminates the use of water in the kernel separation process. Additionally, it eliminates the use of clay in the kernel shell separation process. The efficiency of separation ranges between 90 per cent and 95 per cent, depending on the cracking efficiency. It is suitable for separating palm kernel shells.
Two levels of beneficiaries are targeted. The first would be agro-industrial machinery fabricators who can be trained to fabricate the equipment for sale to palm kernel oil producers. Second, the numerous women and women’s groups scattered all over the country and nearby countries who are involved in palm kernel oil production.
- Best processing practices indicators for artisanal mills to produce high quality crude palm oil was released in 2012.
Attributes: Minimum boiling/sterilisation time of two hours 30 minutes. Keep fruits and ‘digested fruit matrix’ hot throughout digestion and pressing process. Ensure adequate clarification. Ensure adequate sieving to reduce dirt or insoluble content.
The technology is suitable for grain drying and food processing. It is used for production of crude palm oil that meets standards. It minimises postharvest storage of fruits prior to digestion to three to five days.
Source: Manual of Agricultural Technologies developed by
CSIR, MAG and MoFA
Page: 137-140